Award-Winning Records
History of Winning the Association Award from the Japan Powder Metallurgy Association
The products that were highly evaluated by the Japan Powder Metallurgy Association are introduced here.
Diamet will continue to create new value through powder metallurgy.
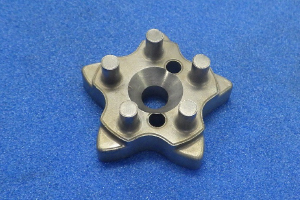
A sintered part for the transmission for motorcycles
This product was highly rated in that a part of the sinter-forged area was made through general sintering, and the density of the pins of 7.4 g/cm3 was achieved with ingenuity.
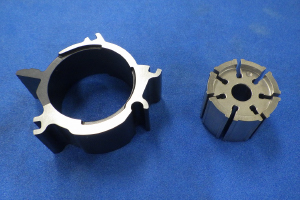
Development of parts for variable capacity oil pumps:Cam ring (left) and vane rotor (right)
These are a family of products consisting of a cam ring and a vane rotor used in variable capacity oil pumps for engines that are becoming widely employed as a technology to enhance the fuel efficiency of automobiles. This family of products requires high precision, high strength, and wear resistance and was highly rated for mass production that was achieved by devising raw materials, manufacturing processes, and processing methods.
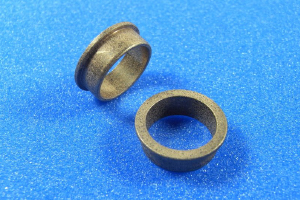
Development of an oil-impregnated sintered bearing for electric parking brakes (EPB)
This product is an oil-impregnated sintered bearing that is used in the reducer section of electric parking brakes (EPB) for automobiles. Although high durability is required for this product because it must be used in a limited space and under severe conditions and must also guarantee the long-term reliability of the operation of brakes, it was highly rated in that mass production at low cost was achieved by devising mold shape, manufacturing method, and the selection of impregnation oil.
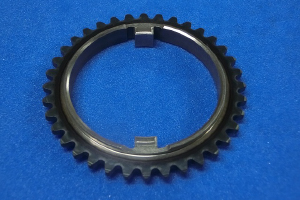
Development of a sprocket drive for fuel-efficient automatic transmission oil pumps
This product was highly rated for achieving a flatness of 0.05 mm without any additional working even though it was a thin-walled product after high-frequency hardening that is likely to cause breakage or deformation, as well as because a sintered material was used instead of a sheet metal to reduce cost by 15% to 20%.
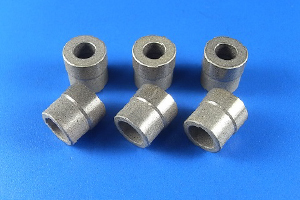
An iron and copper-based oil-impregnated sintered bearing with superior high surface pressure and wear resistance
Although this product is made with a conventional iron and copper-based material, it was highly rated because we controlled the metallographic structure to satisfy requirements and developed a material with the intended properties. In particular, dimensional control becomes more difficult with an increase in the amount of copper and optimizing it by changing the raw materials selected and the sintering conditions is expected to require many trials and errors. This product was highly rated in that we controlled those factors, and its applications are expected to increase in the future.
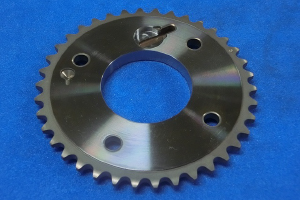
Development of a sizingless thin-walled sprocket
This product was highly rated in that costs were reduced by 15% to 20% compared to sheet metals for sintering. In recent years, inspection costs tend to increase because of 100% inspections to ensure quality control. We succeeded in creating a thin-walled product with a large diameter of over 100 mm in a manner that requires no sizing and electromagnetic exploration; this is a development that acts as a model for other products in the future.
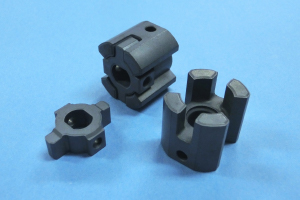
Sintering of a motor joint set for valve lift actuators
This product was highly rated as a high-precision steam-treated product in a sizing-less manner by controlling deformation caused by a spring back due to compacting through optimization of the die assembly material and compacting conditions, as well as by enhancing precision through optimization of the sintering conditions and methods.
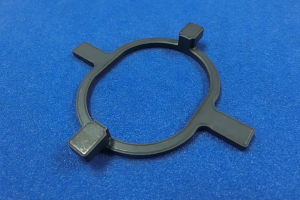
A thin-walled air-conditioning compressor part used in electric vehicles
This product was highly rated for the elimination of machining (through molding) and reduction in weight of an Oldham ring with a thin-walled flange, and it is expected to be employed in gasoline-fueled vehicles in the future.
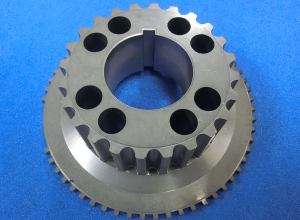
Development of a sprocket with a crank sensor for diesel engines
The contribution to the powder metallurgy industry was highly rated as a result of realizing integration through the sintering method, elimination of machining, and switchover from another manufacturing method.
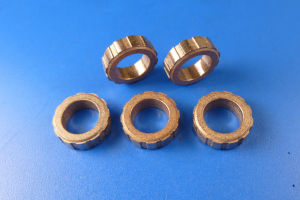
A high-load dry condition-applicable sintered bearing for door closer motor output shaft
The realization of both high strength and high precision, novelty, and uniqueness through the use of a phosphor bronze-based material and then large production volume and its contribution were highly rated.
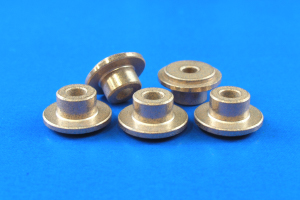
An oil-impregnated sintered bearing for the idle control motor of small motorcycles
The development of a material with strength, sliding property, and oil-retaining property sufficient to withstand fixation through sandwiching was highly rated. In addition, our efforts were also highly evaluated for sizing that achieved high precision, as well as actual performance in mass production.
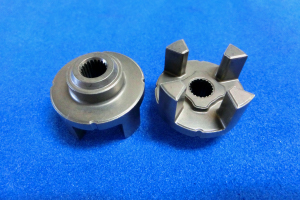
Development of a motor joint for electric power steering
The molding and weight reduction technologies that take advantage of the characteristics of sintering and the increased strength were highly rated. In addition, our success in the switchover from forging to sintering that exhibited the superiority of sintered materials was also highly evaluated.
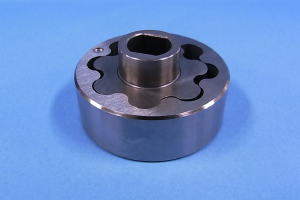
An electric oil pump rotor suitable for use in a quiet environment
The novelty of the new tooth profile applicable to a quiet environment and the uniqueness of the tooth profile design focusing on the gap between the teeth of internal and external rotors were highly rated. In addition, end-users appreciate that it can be mounted in HEV vehicles and idling stop mechanisms and future expansion is expected.
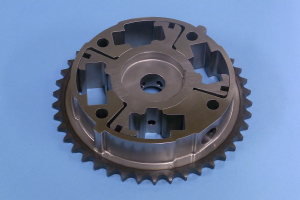
Development of an exhaust variable valve part for eco cars
This product was highly rated because it was designed by taking advantage of the characteristics of powder metallurgy, it eliminated the machining of horizontal bores, eliminated sealing materials, and eliminated the molding of blind holes, as well as the fact that the design combining two parts is effective, and future expansion is expected.
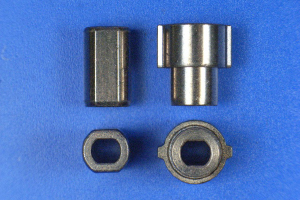
Development of a sintered bearing for poppet valve type EGR
This product was highly rated because we developed a material in which over 6 masses % of graphite was dispersed uniformly to realize mass production, novelty was achieved through imposition sizing of an irregular-shaped inner diameter, switchover from other material was realized through significant cost reduction, and future expansion is expected.
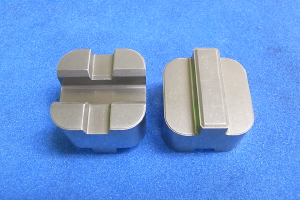
Sintering of a coupling for the engine balancer of clean diesel vehicles
This product was highly rated because the high-hardness material is mass produced with high precision through machining-less net shaping by taking advantage of the characteristics of powder metallurgy, such as securing of the density of protrusions, the manufacturing method was switched from another method, and it is intended for clean diesel applications that are expected to expand in the future.
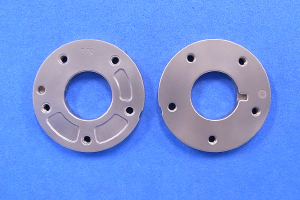
Development of a thrust plate for variable valve timing mechanisms
This product was highly rated in that the assembling surface with a diameter of 77 mm (the flatness equivalent to polished surfaces) was realized without machining through an improvement in the manufacturing process, and the high-precision technology cultivated through this development expanded the range of application of sintered products; market expansion is expected.
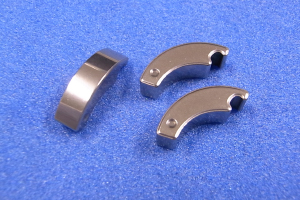
Net shaping of a seat reclining part for automobiles
This product was highly rated for the dimensional accuracy and surface roughness without performing re-compression and machining through improvements in the compacting method and optimization of barrel conditions and because costs were reduced by conducting production through double-cavity compacting and simple processes and the market was expanded.
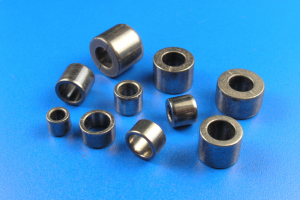
A globally applicable corrosion-resistant bearing material for fuel pumps
This material was highly rated because of superior corrosion resistance, wear resistance, and bearing performance through optimization of material components by taking advantage of the characteristics of sintered materials, the mass production volume is large, and can be expanded globally in the future.
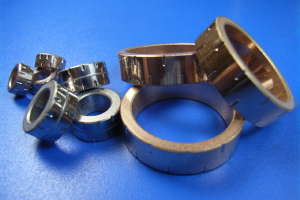
A manufacturing method of sintered bearings suitable for resin insert
This method was highly rated for a shape that prevented the rotation and the falling out in thrust direction of sintered bearing for resin insert, which was manufactured in the sizing process only witout machining, and because the costs were reduced significantly, and the actual production volume was large.
Introduction of affiliated Organizations
Japan Powder Metallurgy Association(JPMA)
The objective of the JPMA is to improve the quality of people’s lives and develop sustainable economy by researching and addressing the challenges of the Powder Metallurgy as well as aiming for the sound development of the Powder Metallurgy Industry.
Japan Society of Powder and Powder Metallurgy(JSPM)
JSPM is a learned society that supports scientific and technological inquiries and innovations in the field of the powder and powder metallurgy.