Products
Diamet’s Oil-Impregnated Sintered Bearings / Sintered Bearings
We manufacture high-precision, high-quality, and high-performance sintered bearings and oil-impregnated sintered bearings that take advantage of our unique powder metallurgy technology and self-manufactured high-precision die assemblies as the top brand in sintered bearings. We also produce oil-impregnated bearings, as well as dry bearings that can be used in a high-temperature or clean environment where oil cannot be used, in addition to high-performance sintered bearings that feature corrosion resistance. Through our unique material, manufacturing, and evaluation techniques, we offer optimum products for a variety of different conditions and environments in accordance with the intended use.
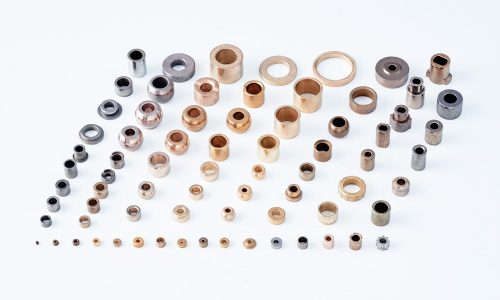
About Oil-Impregnated Sintered Bearings
When compacting and sintering metal powders, tiny pores are generated between particles. The pores of oil-impregnated sintered bearings are impregnated with lubricant. The oil-impregnated sintered bearings contain lubricant in the bearings, so they are functional parts with a self-lubricating function. Because of superior mass productivity and homogeneous properties that are the characteristics of powder metallurgy, they are used in a wide variety of applications, such as bearings for motors.
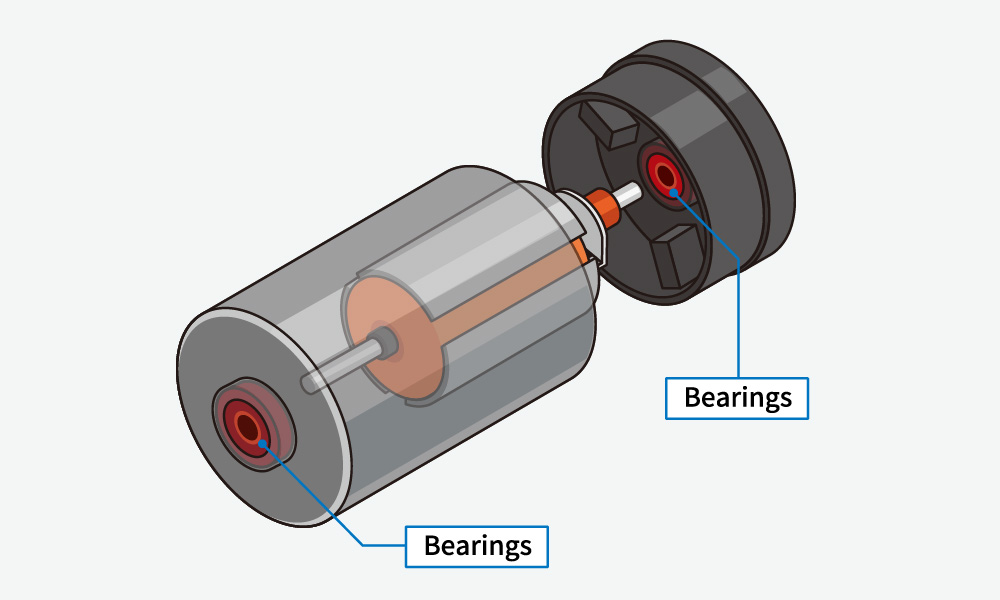
The oil circulation mechanism of oil-impregnated sintered bearings
In an oil-impregnated sintered bearing, a pump action is produced by the rotation of a shaft so that oil is supplied from inside the bearing to the clearance between the shaft and the bearing to form an oil film. Although the oil film leaks into the pores at the bottom of the sliding surface, the oil is circulated in the bearing by the pump action and is then supplied to the clearance between the shaft and the bearing again. When the shaft stops, the oil is absorbed into the pores inside the bearing. This mechanism enables retention of a semipermanent and stable sliding state with no need for constant lubrication.
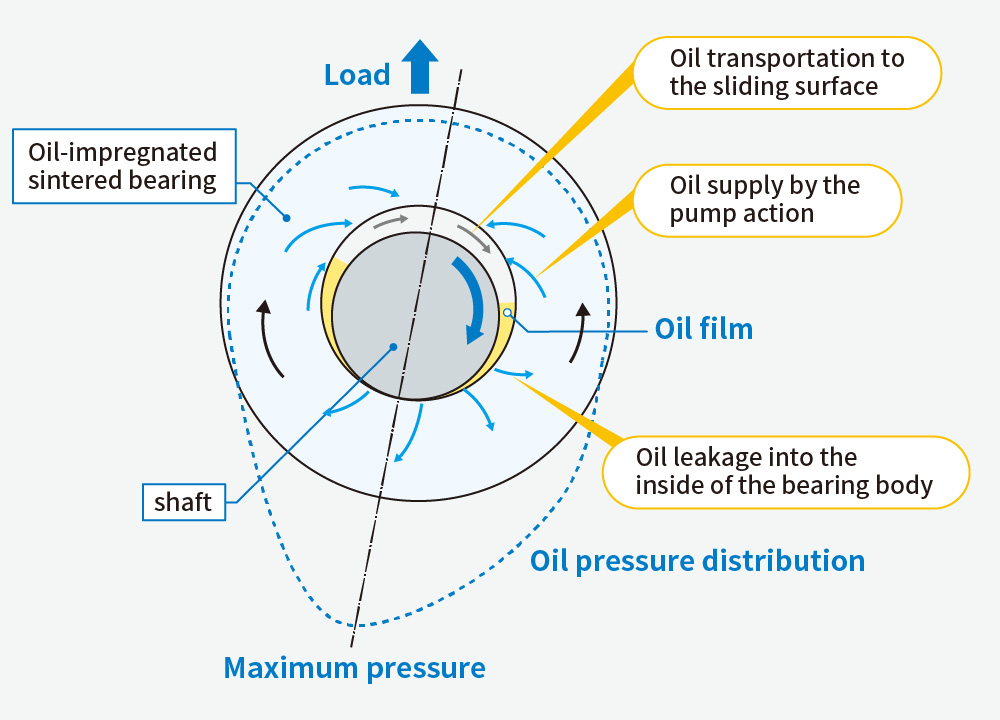
Examples of Use Applications of Oil-Impregnated Sintered Bearings
Power window
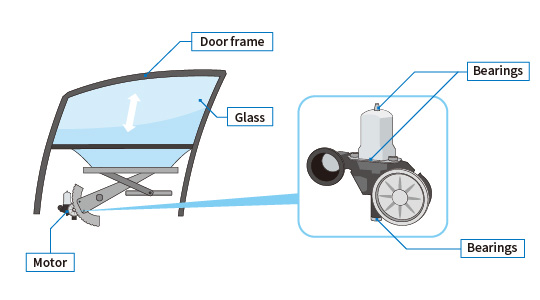
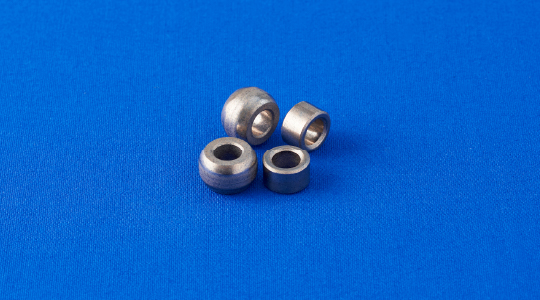
For the bearings in motors that are used irregularly, such as the motors for power windows, it is necessary to form an oil film between the shaft and the bearing instantaneously, even during unstable operation while maintaining sliding performance, as well as to supply reliable material at low cost for severe low speed and high load use conditions. By focusing air permeability and pores on the surface that lead to the formation of oil films to optimize the materials, we successfully developed highly durable, reliable, and cost-effective material.
Starters
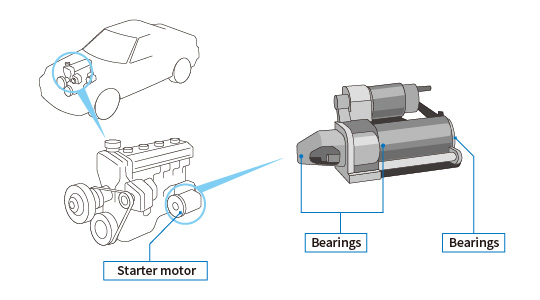
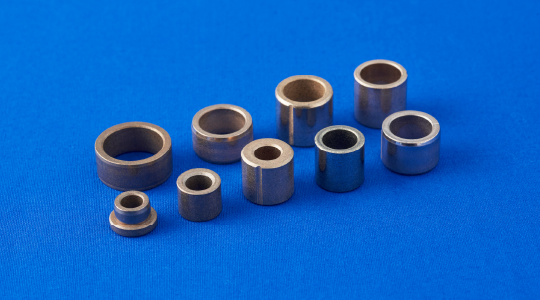
Starter motors start engines. The motor section is designed to rotate at high speeds to generate high torque. In recent years, the need for smaller size and lighter weight has been increasing more than ever before, and oil-impregnated sintered bearings that can withstand high-speed rotation and high torque are required to ensure superior sliding performance, wear resistance, and reliability. Different types of oil-impregnated sintered bearings, such as bearings supporting an armature (a rotating part of an electricity generator with a wire wound around the core), bearings for planetary gears, bearings for the output section, are used in combination in a starter motor, and many of our bearing products are used.
Wipers
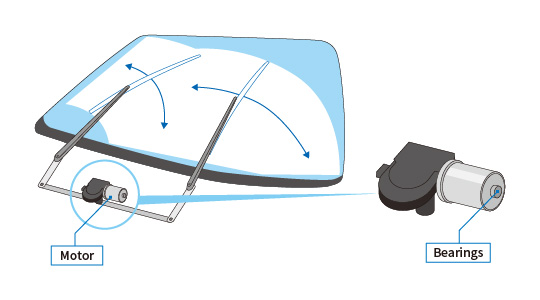
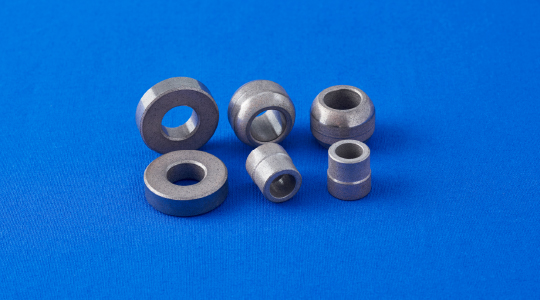
Wiper motors secure visibility by eliminating raindrops and snow from windshields. Because any stoppage due to failure could lead to a major accident, high reliability and wear-resistant materials are required. In addition, because of the need for a decrease in weight and size and the high torque applied to the bearings, high-strength materials are necessary. We offer wear-resistant and high-strength material for oil-impregnated sintered bearings and also provide many bearings for wiper motors.
Fuel pump
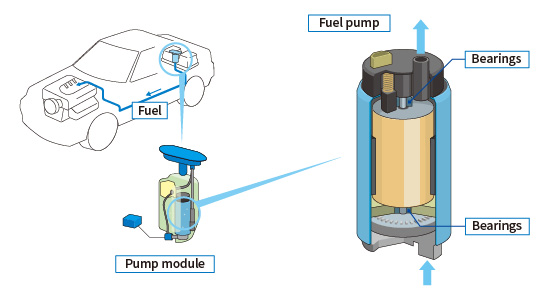
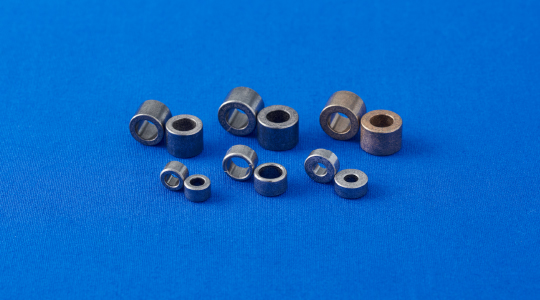
Fuel pumps are built into fuel tanks for putting fuel into engines. They are soaked in fuel at all times, and the bearing properties and corrosion resistance are required under a severe sliding environment against low-quality gasoline containing impurities. Our corrosion-resistant bearings exhibit superior corrosion resistance, wear resistance, and bearing performance even in gasoline containing highly concentrated sulfur or organic acid, and they are used globally and widely.
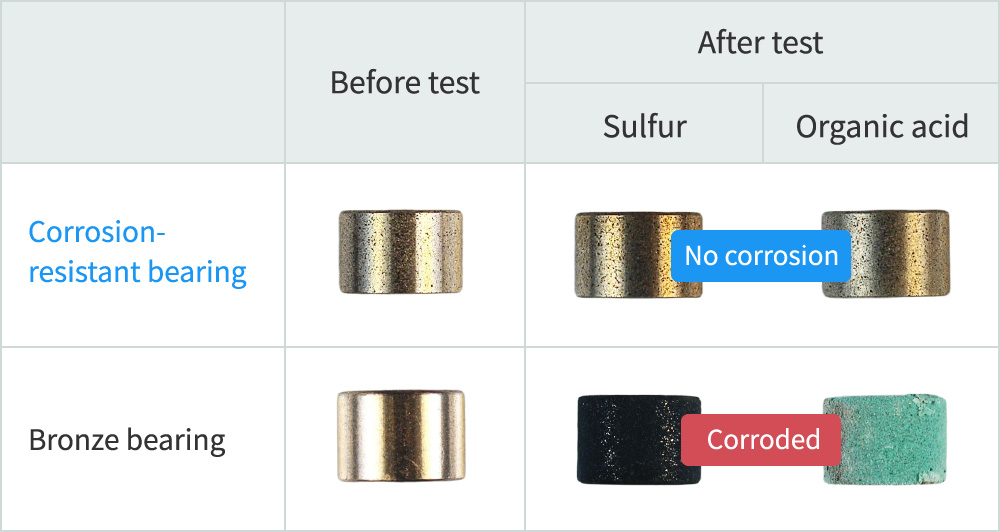
Electronic throttles
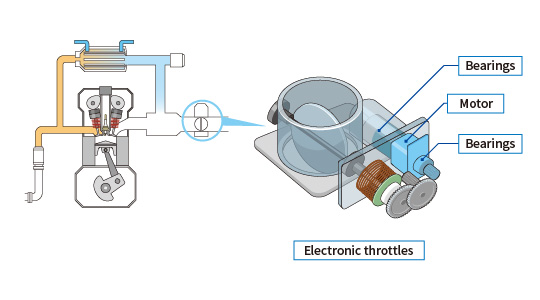
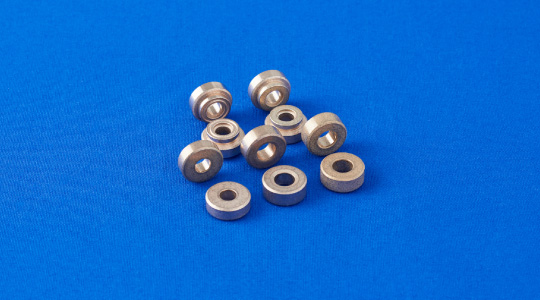
The engine throttle mechanism controls intake air volume and engine output by regulating the throttle opening degree. Conventionally, a throttle was operated by the amount of depression of the accelerator pedal by the driver via a wire. On the other hand, a electronic control throttle regulates the throttle using a motor via an electronic control unit (ECU) based on sensor that measures the degree of opening of the accelerator pedal. Because electronic control throttles offer finer control of the intake air volume than mechanical throttles, an improvement in fuel efficiency and a reduction in harmful exhaust gas can be achieved.
Our bearings are used in motor regulate the degree of opening of the throttle valve. Since electronic control throttles are placed near the engines, they need to be able to function in a wide temperature range and have vibration resistance.
Therefore, the bearing, made by impregnating Fe-Cu based material whose surface is controlled to be Cu rich with special fluorine oil that is applicable to a wide temperature range, must exhibit superior performance in wear resistance, friction coefficient, and seizure resistance and contribute to improvements in fuel efficiency, reductions in harmful exhaust gas, and significant reductions in costs.
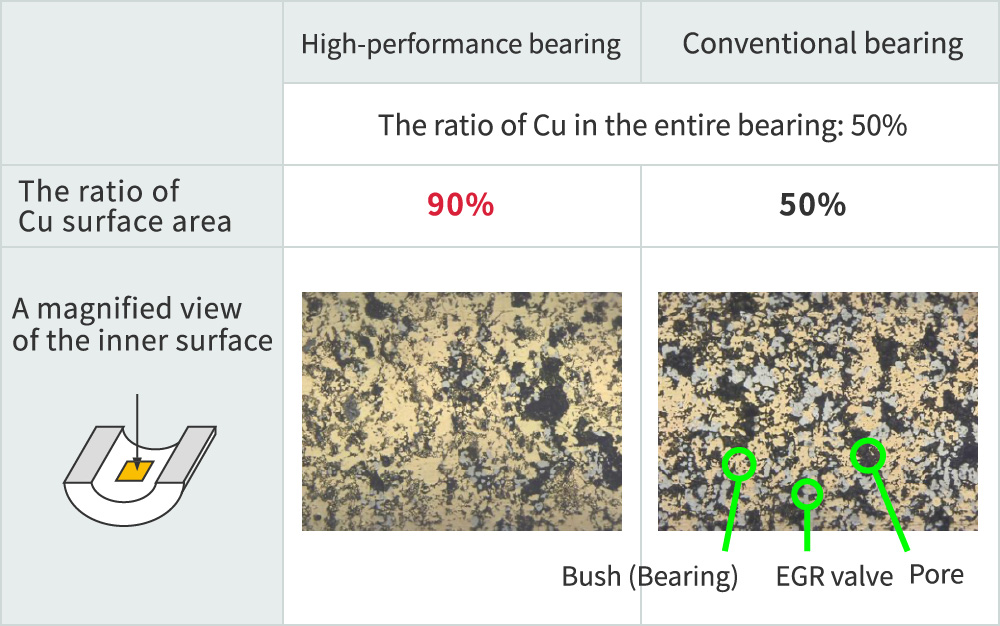
EGR(Exhaust Gas Recirculation)
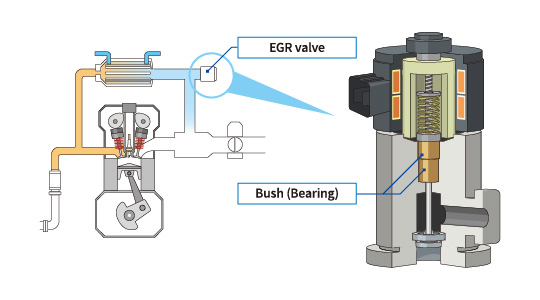
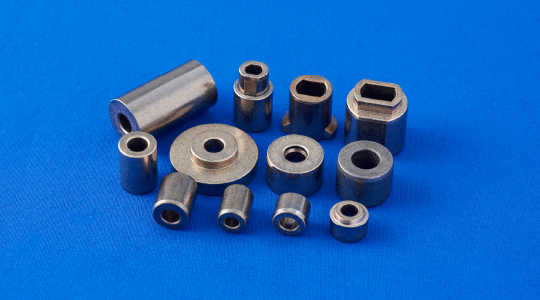
Exhaust gas recirculation (EGR) returns part of the exhaust gas from an automobile engine to a combustion chamber; this system is in widespread use to reduce NOx and fuel consumption. The bush for EGR is used for the valves that lead part of the exhaust gas to the intake air side and is used in an exhaust gas environment with a wide temperature range from ambient temperature to high temperatures where lubricants cannot be used. Therefore, we have realized material with superior self-lubricating property at high temperatures and oxidation resistance by adding a large amount of solid lubricant to the bearing material, which contribute to a reduction in NOx emitted and the fuel consumption of automobiles.
Sintered Bearing Forming Technique (patented)
Bearings for resin inserts
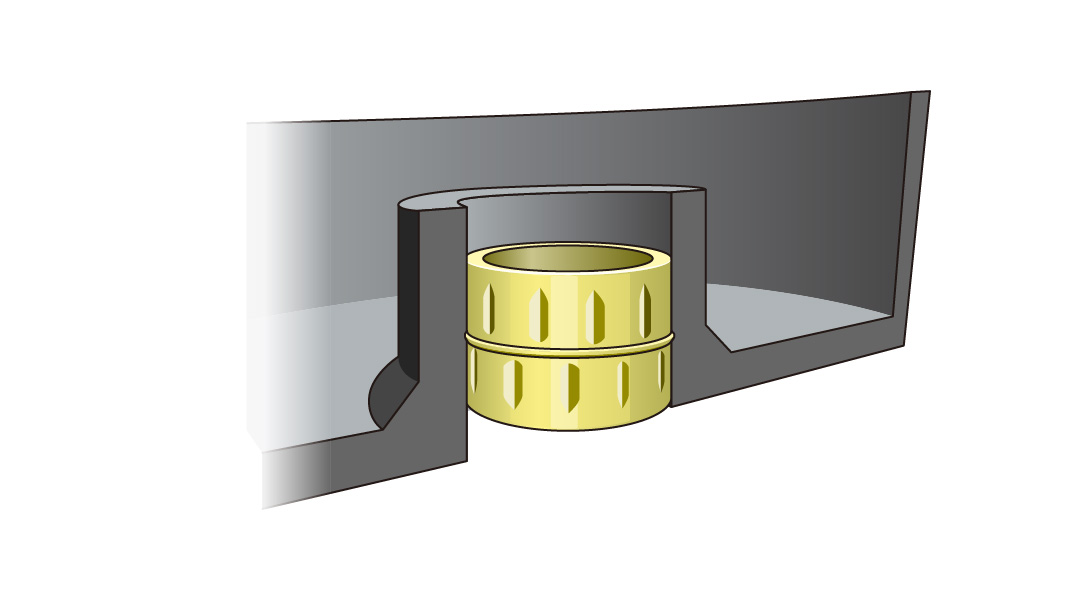
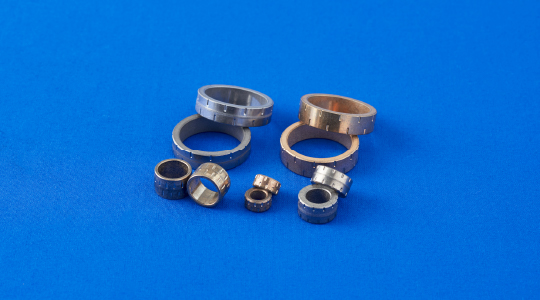
Although sintered bearings are generally press-fit into housings for use, housings are increasingly resinified and associated with the reduction in costs and the weight of motors. As a result, the need for sintered bearings that are suitable for resin inserts has been increasing. Because resin inserts have lower fastening power compared to press-fitting, it is necessary to implement measures to prevent the bearings with such inserts from rotating and falling out the thrust direction.
In the typical examples of bearings that have already been put into practical use, grooves were formed in the axial direction on the outer periphery of the bearings to prevent rotation, and grooves were also machined in the circumferential direction on the outer periphery to prevent falling out in the thrust direction. Although a reduction in costs was one of the purposes of the resinification of housings, a significant increase in bearing prices due to machining was a problem for customers. Therefore, we developed sintered bearings suitable for resin inserts that are formed in the process to prevent rotation and falling out in the thrust direction without any machining by using our unique forming technique. These bearings are increasingly used each year and contribute to cost reductions by customers.
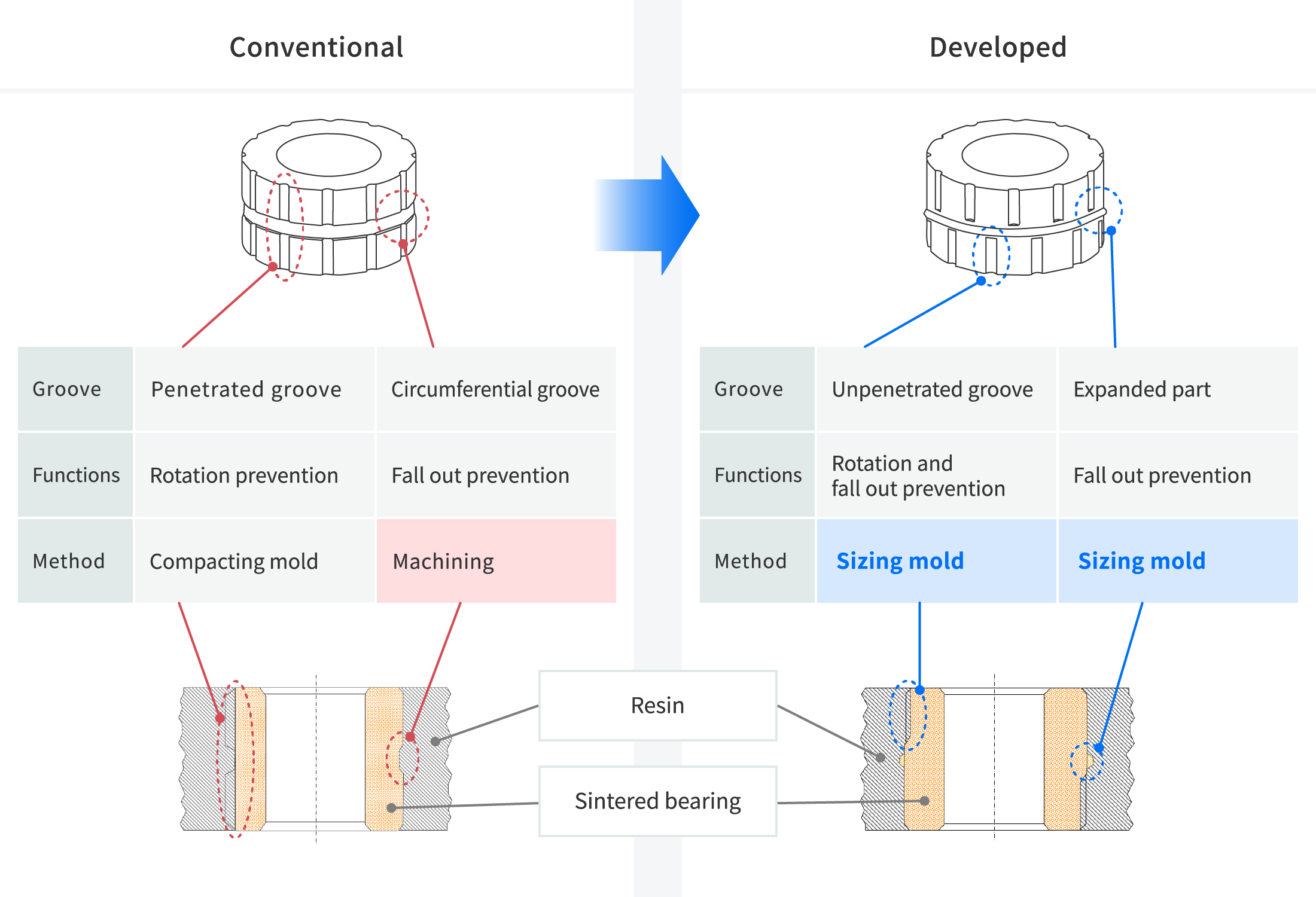
Application as sliding materials
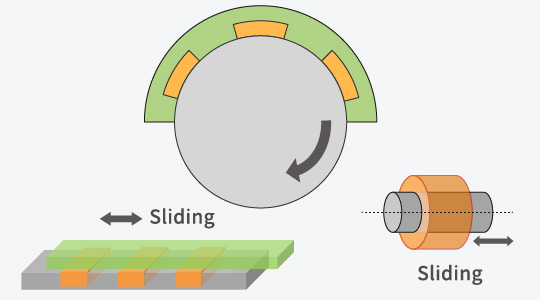
Our bearings can be used for rotating shaft and as sliding materials.
Materials list for Oil-Impregnated Sintered Bearings / Sintered Bearings
About Sintered Machine Parts
The sintered machine parts that we manufacture through the powder metallurgy method are used in a variety of applications—engine parts, transmission parts and different types of sensors. By taking advantage of high precision, complicated shapes, and high productivity, which are unique to the powder metallurgy method, we offer iron- and stainless steel-based products according to demand characteristics at low costs.
Sintered Machine Part Products
Variable valve parts
We manufacture components for variable valve timing mechanisms. For these parts that require high precision and strength, we contribute to the reduction in product costs through the realization of complicated shapes with multistage compacting technology, elimination of machining processes by forming with high-precision die assemblies, and increases in strength with the high-density manufacturing method.
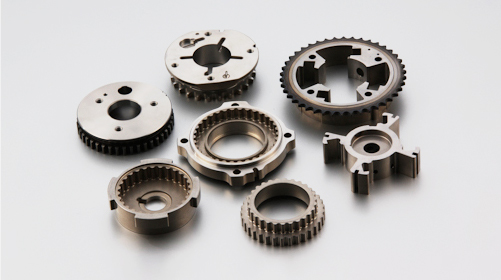
Sprockets and pulleys
We offer machining-less, low-cost, and high-precision sprockets and pulleys. We mainly manufacture roller chain and silent chain types of sprockets. In particular, we apply densification technology to silent chain type sprockets that require high strength to consistently provide high performance products.
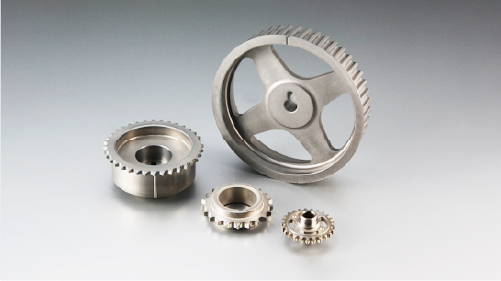
Oil pump rotors
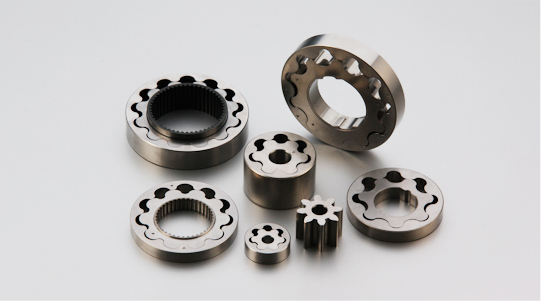
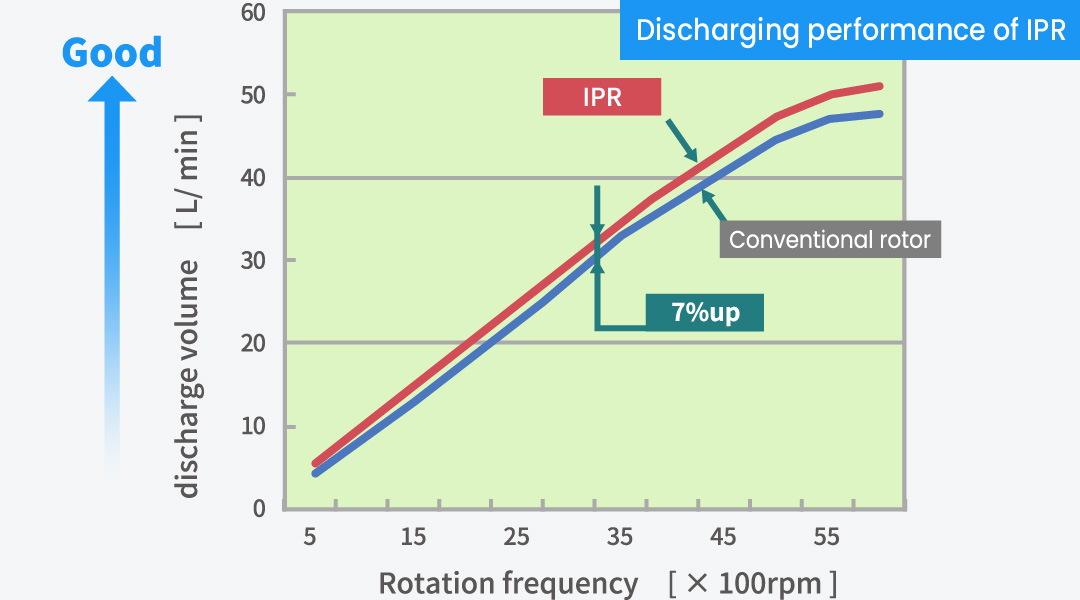
IPR® (Intelligent-Profile-Rotor) is our original sintered oil pump rotor with a patent-pending tooth profile characterized by high discharge efficiency, low friction, and low noise. The rotor contributes to the realization of low fuel consumption and superior quietness. By taking advantage of high efficiency, we produce high performance in the manufacture of compact rotors in electric oil pumps. Furthermore, as a design service, we customize tooth profiles and propose port shapes according to customer needs.
Transmission parts
We manufacture parts for automatic transmissions (AT), manual transmissions (MT), and continuously variable transmissions (CVT). To meet the needs for high precision, high strength, and complicated shapes, we offer products ranging from compact ones to large ones as desired at low costs.
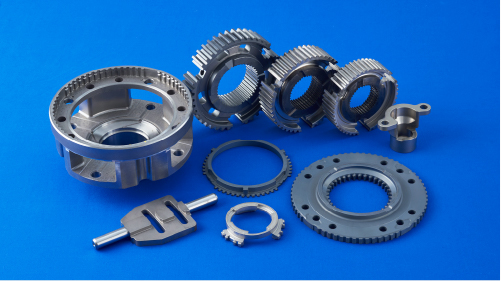
Sintered Stainless-Steel Part Products
We manufacture sintered stainless-steel parts such as exhaust system components and sensor rings for brakes. Because such parts are used in severe high-temperature environments, high corrosion resistance and anticorrosion properties are required. We offer products in accordance with different usage environments and demand characteristics at low cost.
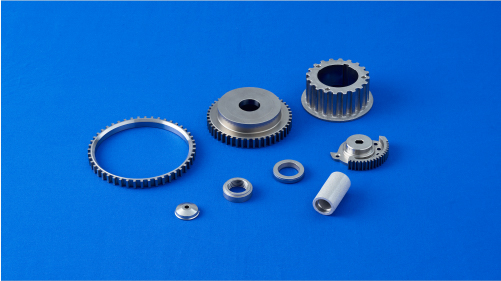
About Soft Magnetic Materials
Powder magnetic cores are characterized by high electric resistance and low loss because every single metallic magnetic powder particle used is insulated. In addition, compared to magnetic steel sheets, they offer high flexibility in shaping and can be downsized. We develop and manufacture powder magnetic cores with high magnetic flux density and low iron loss with our unique insulation film technology.
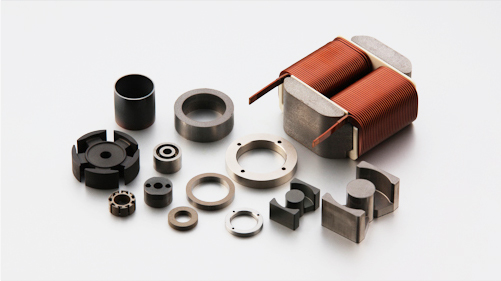
Soft Magnetic Material Products
Cores for boost reactors
Boost reactors are used in circuits that increase electric voltage to the level required to drive motors. We manufacture block cores, U cores, E cores, PQ cores, and cores with different shapes.
*A power control unit for a hybrid automobile
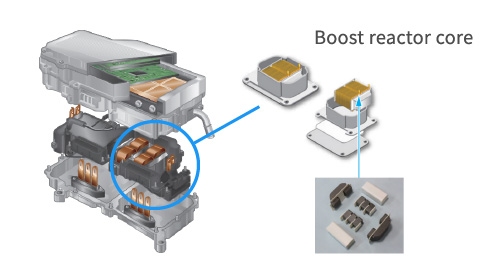
Cores for motors
We impart dimensional shapes that cannot be realized with magnetic steel sheets to achieve the downsizing of motors. We can shape cores for axial gap motors, brimmed cores for radial cap motors, and claw-pole cores.
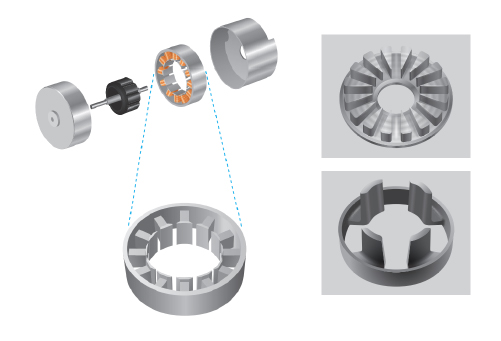
Cores for high-frequency
Cores for high-frequency are used in industrial equipment, as well as DC-DC converters and onboard chargers for electric vehicles (xEV) including hybrid electric vehicles (HEV) and battery electric vehicles (BEV). We are in the process of developing alloy cores that are compatible with several tens to several hundreds of kHz.
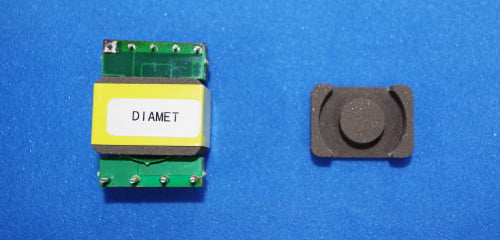
Materials list for powder magnetic
We provide custom services ranging from selection of soft magnetic materials to design and commercialization according to applications and characteristics.
Series | Materials | Types | Magnetic properties | Application | |||||||||||
---|---|---|---|---|---|---|---|---|---|---|---|---|---|---|---|
Maximum relative permeability | Magnetic flux density | Iron loss | |||||||||||||
2kA/m T |
10kA/m T |
1T/ 400Hz kW/㎥ |
0.1T/ 10kHz kW/㎥ |
0.02T/ 100kHz kW/㎥ |
0.02T/ 300kHz kW/㎥ |
||||||||||
MF | MF10 | Sintered Mgnetic Materials | 1,500 | 1.30 | 1.53 | ― | ― | ― | ― | Motor Relay Solenoid | |||||
MF19 | 3,000 | 1.40 | 1.61 | ― | ― | ― | ― | ||||||||
MBS | MBS-S20 | Powder magnetic core | 700 | 1.22 | 1.67 | 470 | ― | ― | ― | Motor | |||||
MBS-F20 | 350 | 0.82 | 1.47 | 420 | ― | ― | ― | ||||||||
MBS-418 | 500 | 1.04 | 1.60 | 410 | ― | ― | ― | ||||||||
MBS-207 | 550 | 0.94 | 1.48 | 380 | ― | ― | ― | ||||||||
MBS-450 | 500 | 1.05 | 1.55 | 230 | ― | ― | ― | ||||||||
MBS-R | MBS-RL200 | 250 | 0.62 | 1.36 | ― | 170 | 130 | 615 | Inductor | ||||||
MBS-R3 | 200 | 0.48 | 1.27 | ― | 130 | 115 | 650 | ||||||||
MBS-RA | MBS-RA5 | 150 | 0.38 | 0.99 | ― | 100 | 70 | 400 | |||||||
MBS-RXA6 | 70 | 0.18 | 0.57 | ― | 35 | 30 | 240 | ||||||||
MBS-RXA7 | 45 | 0.11 | 0.40 | ― | 33 | 20 | 90 |